Wie is TPprojecten nu eigenlijk.
Algemeen
Mijn naam is Twan Peeters en inmiddels heb ik 48 jaar werkervaring op mijn teller staan. Met mijn ervaring van 48 jaar in de techniek ben ik voor u de juiste partner voor het maken van calculaties, engineeringsopdrachten en projectleiding. Mijn kennis gecombineerd met mijn ervaring zal uw projecten tot een succesvol einde brengen. Hebt u een klant die iets heeft bedacht, een idee heeft, wil sparren met een ervaringsdeskundig, en wil dat graag door u hebben uitgewerkt en een budget ontvangen, dan bent u bij mij op het juiste adres. Daarbij ga ik u helpen!
Oh ja, zeker niet onbelangrijk, een lieve vrouw en 3 fantastische meiden. Allemaal goed terecht gekomen en ben ik de trotse opa van Scott.
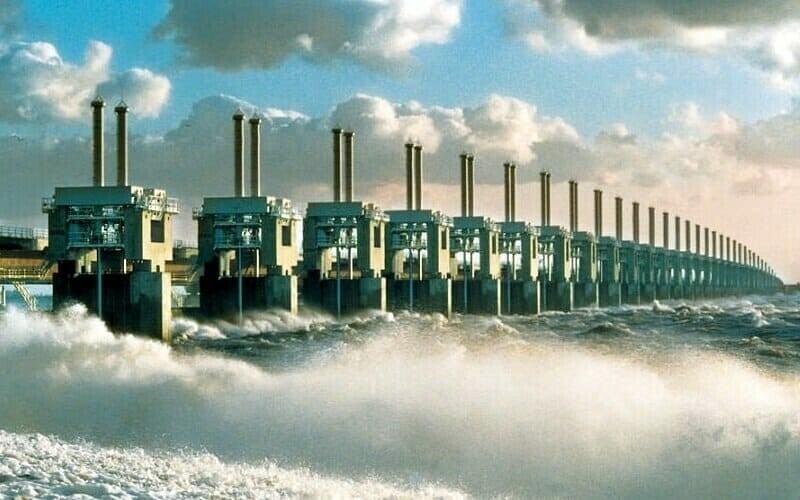
Mijn eerste jaren bij Sif
Als heel jongen vent ben ik gestart als OP (onderpoeder) lasser bij SIF in Helden Panningen. Mijn werkzaamheden bestond uit het OP lassen van buizen voor de sluizen van de Oosterscheldekering ook beter bekend onder de naam Neeltje Jans.
En zoals altijd kwam van het een het ander, ik werd de troubleshooter, machinebouwer, programmeur, paneelbouwer, kabelaar en inbedrijfnemer van mijn eigen gebouwde installaties. Toen de Directie voor enkele miljoenen aan lasapparatuur had gekocht bij Esab in Zweden kreeg ik de vraag als ik een van de 5 machines wilden opbouwen. Het werd een rondnaadmachine. Mijn taak werd om te kijken wat er moest gebeuren om de machines te kunnen inzetten met 2 laskoppen en bediend door een operator. Het lassen met 2 koppen en een bediener was een, het andere, en veel belangrijker was het 24/7 kunnen inzetten van de machine. Daar begon het ontwikkelen van laskoppen met speciale laspitten die 24/7 konden worden ingezet. De besturing werd door mij aangepast en op een gegeven moment was de machine "free for production". Dit duurde enkele jaren, en voor ik het in de gaten had zat ik dagelijks bij de directie te brainstormen over welke machines nodig waren om een project te kunnen maken. Hoe we de inschakelduur konden vergroten en de neersmelt (aantal Kg per uur) konden verhogen. Dit zorgde weer voor een PLC applicatie die van iedere machine de werkelijke lastijd deed meten en wegschreef in een file. In de morgen kwam de technisch directeur een rondje maken en bij een druk op de knop kwam er een lijst met gelaste tijden per machine uit. Dit zorgde weer voor nieuwe uitdagingen zoals het aanpassen van lasdraad van 25Kg naar drums van 250Kg, van een draad naar 2 draden van 2 naar een extra wisselstroom draad etc.
Door dat ik steeds vaker bezig was met het bedenken van oplossingen moest ik steeds meer werkzaamheden bij onderaannemers onderbrengen. En werd mijn uitvoerend werk steeds minder en werd ik de organisator en bedenker van de benodigde machines. Eigenlijk was niks meer vreemd en kwamen gerenommeerde bedrijven zoals Smitweld en Esab met mij brainstormen over hoe hun installaties moesten worden gebouwd en hoe we ze 24/7 betrouwbaar konden maken.
Wat maakte je dan zoal wordt mij vaak gevraagd en dan zeg ik "alles wat nodig was om een project te realiseren" of een oplossing omdat bestaande procedures vanwege milieu technisch of proces technisch niet meer konden. Daaruit ontstond de mobiele Frees voor het maken van lasnaden op elke locatie in de productiehallen.. Dit was een oplossing die er voor zorgde dat lasnaden werden gefreesd waardoor er zo min mogelijk vulling nodig was met lassen.. Dat werd de zogenaamde Narrow gap naad. Onderin R8 mm en dan met 6 of 8 graden omhoog, variërende in plaatdiktes van 50 tot 250mm.
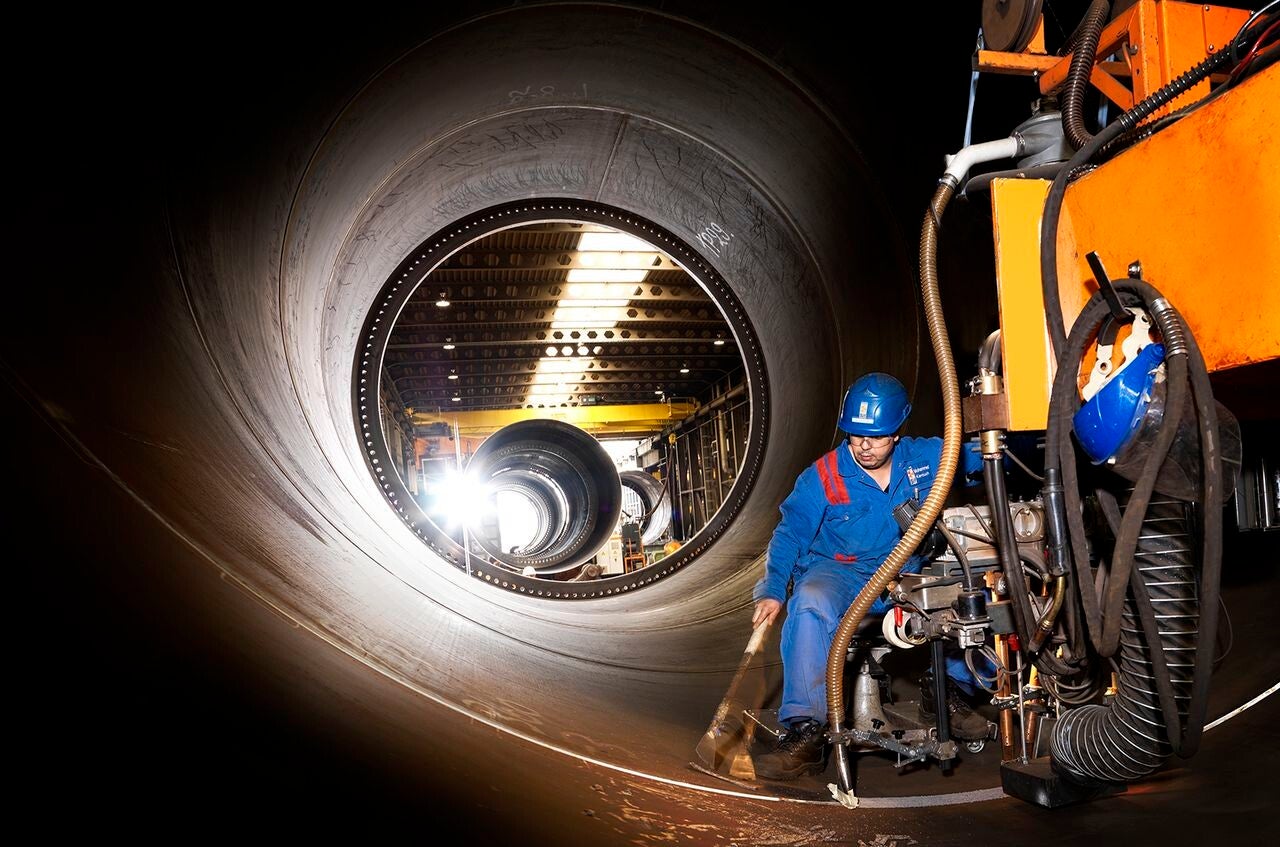
Rondnaad inwendig
Rechts een van de vele ontwikkelde machines van destijds voor het maken van rondnaden inwendig. Een lange arm op een rijdende wagen die naar binnen kan rijden met voorop een enkele laskop met twindraden.
Op een gegeven moment door vertrek van de Hoofd Technische Dienst kreeg ik de vraag als ik de technische dienst wilden gaan runnen als HTD. Dat was het moment dat het bezig zijn met techniek veranderde in het bezig zijn en gaan met mensen in je team. Dit was natuurlijk een geweldige ervaring en was je bezig om mensen te stimuleren om preventief onderhoud te doen. Dit was natuurlijk niet voor iedereen vanzelfsprekend en ging het langzaam van schouderklopjes omdat je iets snel had opgelost naar schouderklopjes omdat alles storingsvrij had gelopen. Als ik het hier schrijf lijkt het heel eenvoudig, maar ik weet dat het een hele onderneming was iedereen op de zelfde lijn te krijgen.
Onderhoudsschema's werden bedacht, operators kregen taken in "first trouble shooting" en de TD volgde dit op. Storingslijsten werden gemaakt en in de PC verwerkt om te kijken welke storingen veelvuldig voorkwamen en wat we daar aan konden doen. TD mensen konden zich verder ontwikkelen en het team groeide uit tot een gesmeerde machine. Verder had ik natuurlijk mijn vaste taken zoals het:
Laten uitvoeren van (preventief) onderhoud aan machines in installaties
Coördineren van dagelijkse bedieningswerkzaamheden aan installaties
Leidinggeven en coachen van technisch medewerkers
Onderzoeken van frequente technische problemen en aandragen van verbeterplannen om deze in het vervolg te voorkomen
Waarborgen van continuïteit en kwaliteit van het (productie)proces
Projectmatig aanpakken van investeringen ter verbetering van de machines, installaties en productielijnen
Meedenken over verbeteringen en optimalisatie van bestaande processen
Sturen en controleren van eventuele externe onderhoudspartijen op basis van afgesloten contracten en planning
Bijhouden van een administratie waarin uren, materialen, tekeningen en andere documenten met betrekking tot de het (productie)proces geregistreerd worden
Opmaken van periodieke rapportages ten aanzien van het functioneren en optimaliseren van de machines en installaties
Toetsen van machines en installaties aan wettelijke verplichtingen
Opstellen en bijhouden van meerjarig onderhoudsplannen en bijbehorende kostencalculatie
etc.
Maar na 5 jaar als HTD bezig te zijn miste ik uiteindelijk wel het gevoel met de techniek en besloot ik een nieuwe uitdaging aan te gaan. En ergens in 98 heb ik mijn baan opgezegd en opzoek gegaan naar een nieuwe uitdaging in de techniek.
Van Sif naar Unica Industry Solutions
De kalender staat op augustus 1998 en ik ben aangenomen als assistent projectleider bij Stroeken-Electro in Tegelen. Een gerenommeerde en gerespecteerde installateur op het gebied van zowel Utiliteit als Industrie. En Industrie was er meer als voldoende in Tegelen en omgeving. Denk aan de dakpannen fabrieken, ijzergieterijen, aluminiumgieterijen, de Globe, Egidius Janssen, (de ontdekker van de klappersluiting) Poeth, Scheuten Glas, Canon, Oerlemans Foods etc.
Het uiteindelijke streven was om binnen afzienbare tijd als Senior projectleider aan de slag te gaan. Het eerste jaar heb ik meegelopen met mijn voorganger en ontzettend veel geleerd. Bij Sif was ik de vraagbaak en iedereen met een vraag over machines, lassen of iets anders kwam bij mij terecht.
Wat mij op dat moment duidelijk werd is dat ik na de overstap ontzettend ben gaan groeien in de breedte. Technieken die ik niet eerder had meegemaakt, een diversiteit aan klanten dat het nooit zou gaan vervelen.
Mijn eerste grote klus was het offreren van een vlakkenstapelaar voor Isover te Etten-Leur, die werd gebouwd door machinebouwer Boral uit Tegelen. Nadat de offerte was uitgebracht en de klant uiteindelijk de stapelaar had gekocht begon de Engineering van de installatie. Het betrof een installatie die uniek was in zijn uitvoering en geschikt voor alle plaatafmetingen die Isover kon maken op de D-lijn. De installatie bestond uit een aanvoersectie, klep, inloopstation, overzetter, kantelaar opvoerband, telescoopbanden, stuwklep, hefrooster, rollenbaan, palletinvoer, platenuitvoer en draaistation. Een hele mond vol maar een geweldig project. Uitgangspunt was 60 platen van 1200x600 per minuut stapelen. De besturing was een Telemecanique PLC met een ASI bus. Dit was omdat de kantelaar middels een sleepring werd aangesloten en de ASI bus daar goed mee om kon gaan zonder storing. Bediening was een TXT touchscreen met functietoetsen en Touch bediening.
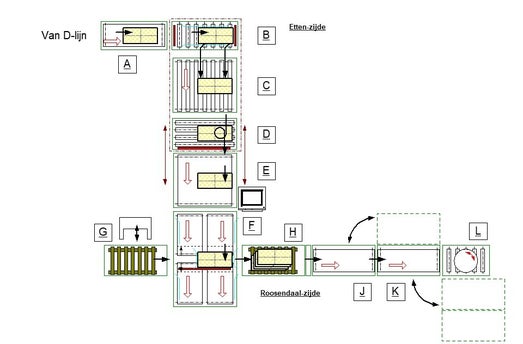
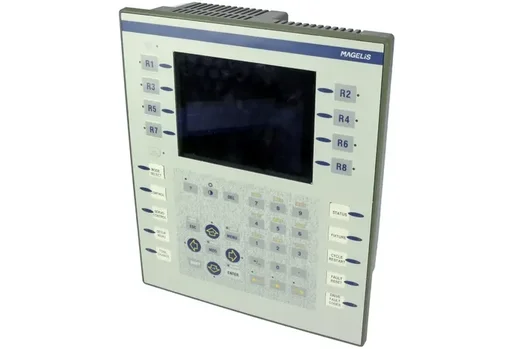
Algemene werking van de installatie:
Vanaf de D-lijn worden de losse of samengestelde vlakken (door slagschaar in rechthoekige delen gekapte vlakken) aangevoerd. De producten lopen via de transportband (A) op een rollenbaan (B) tot tegen een stuwplaat.
Een armenset licht het product op en tilt het vervolgens op de riementransporteur (C), zodat de transportrichting 90° wordt gekeerd.
Vanaf de riementransporteur lopen de glaswolvlakken naar een kantelstation (D). Hier kunnen de vlakken desgewenst ondersteboven worden gedraaid, bijvoorbeeld om de vlieszijde te keren. Dit is van belang voor de stapelpatronen en is vastgelegd in het ‘recept’, zie paragraaf 5.3.
Vanaf het kantelstation worden de vlakken via transportband E naar het stapelstation (F) gevoerd. Deze is voornamelijk samengesteld uit vier transportbanden welke uit elkaar worden getrokken om de vlakken verticaal af te voeren naar een tweetraps-stapelunit.
Een pallettoevoerstation (G) separeert steeds één pallet en voert deze tot onder het stapelstation. Daar worden de glaswolvlakken in de tweede stapelfase op de pallet gestapeld.
De gevulde pallets komen via een veiligheidslichtscherm uit het stapelstation en arriveren op een rollenbaan (H). Daar moeten ze door een heftruck worden afgevoerd.
Het is ook mogelijk dat de glaswolvlakken niet op een pallet worden gestapeld maar tot een zelfdragende stapel. In dat geval worden de stapels achter de rollenbaan (H) door-getransporteerd, via twee tussentransportbanden (J en K) naar een keerstation (L). Daar kan een 90°-rotatie in het platte vlak worden uitgevoerd om de stapels in de juiste richting af te voeren naar de inpaklijn. Deze inpaklijn maakt geen deel uit van de hier omschreven stapelaar.
Het volgende project werd een vliesafwilkkelbok voor Isover Duitsland gevestigd in Duitsland. Het vliesafwikkelstation ontwikkeld voor het
toevoeren van 1 of 2 lagen glasvlies aan een productielijn voor glaswol. Iedere vlieslaag wordt vanuit een afwikkelhaspel en via enkele omleidrollen en een baanspanningsregeling aangevoerd. De afwikkelhaspels zijn uitgevoerd met een 2-voudige rolopname met automatische hechtfunctie, zodat de rolwisseling kan worden uitgevoerd bij doorlopende productie. De nieuwe vliesrollen worden via een wagen aangevoerd, het plaatsen van de rollen in de (lege positie van de) haspel gebeurt semiautomatisch. Na productwissel of vliesbreuk moet het begin van het vlies handmatig en op lage snelheid door de baanspanningsregel-walsen worden gevoerd. Het station is uitgelegd voor het aanbieden van smalle en brede vliesrollen.
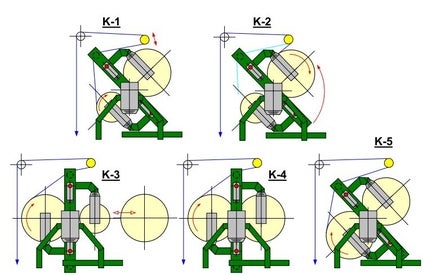
En zo ben ik 26 jaar bezig geweest met allerhande projecten in Nederland maar ook in het buitenland. Uiteenlopend van de hierboven omschreven machines tot en met een Biogascentrale, een nieuw silogebouw, drogerinstallaties in de fritessector, banden recycling, mestopwerking, schietbanen, transportsystemen, een nieuwe aanzetafdeling en complete conveyor systemen.
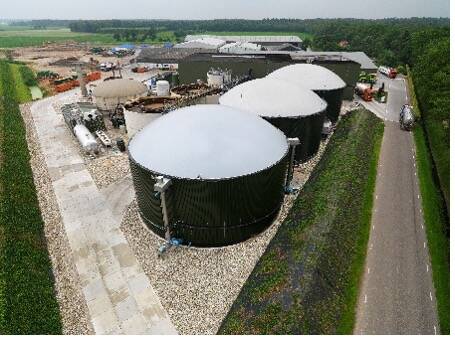
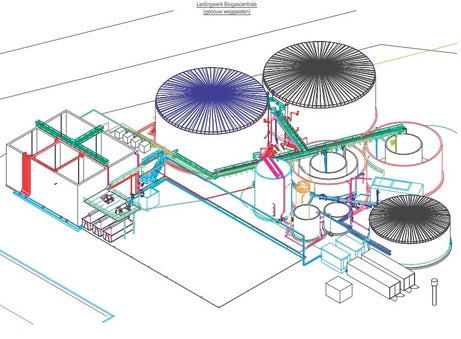
Peter Greven
Het geheim van een goed huwelijk;
Wat hebben Unica en Peter Greven, producent van oleochemische halffabricaten in Venlo, met elkaar gemeen? Het zijn allebei familiebedrijven met een lange historie; Peter Greven bestaat 100 jaar en Unica 90 jaar. Ook geloven beide bedrijven in de kracht van duurzame klantrelaties.
Twan Peeters is projectmanager en salesverantwoordelijke bij Unica Industry Solutions Venlo (UIS). In 2023 vierde hij zijn 25-jarig dienstverband bij Unica. Opvallend genoeg duurt zijn verbintenis met opdrachtgever Peter Greven al bijna net zo lang. Twan: “Ik werkte nog voor Stroeken-Electro – dat in 2008 werd overgenomen door Unica – toen we voor Peter Greven de eerste lijn mochten ombouwen. Dat was een groot project met vele uitdagingen. Maar we wisten de klus te klaren en het vertrouwen van de klant te winnen.”
Continu aan de bal
Sinds die tijd is Unica continu aan de bal, zegt vestigingsmanager Joop van der Sterren van UIS Venlo. “Peter Greven is een waanzinnig mooi bedrijf. We komen er dagelijks over de vloer: voor kleine, middelgrote en eens in de paar jaar een groot project. In 2012 hebben we een tweede dp-lijn integraal opgepakt. Momenteel leveren we een compleet nieuwe fabriek op. De dispersie aanmaak plant is een kopie van de bestaande installatie, maar dan groter en beter. We zijn nu bezig met het testen en inbedrijfstellen. Tot nu toe gaat het goed en is de klant tevreden.”
Moeite doen
Dat is volgens Joop grotendeels te danken aan de inspanningen van zijn jubilerende projectmanager. “Twan heeft zoveel domeinkennis: hij kent de locatie van haver tot gort. Ik durf zelfs te beweren dat hij beter weet waar alle kabels lopen dan de medewerkers van Peter Greven zelf.”
Twan lacht bescheiden. Hij neemt zijn werk serieus en vergelijkt klantrelaties met een huwelijk. “Er gaan dingen goed en dingen fout. Samen ben je continu bezig om de relatie te verbeteren. Daarvoor moet je elkaar vertrouwen, blijven communiceren en moeite doen om er samen uit te komen.”
One stop shop
Unica weet steeds beter waar de industrie in Nederland behoefte aan heeft. Joop: “Ik ben enorm trots op de grote hoeveelheid technische disciplines die we in deze oplossing laten zien. Van piping, stoomtechniek en high tech software tot technisch beheer, onderhoud, legionellapreventie en NEN3140-inspecties door Unica Building Services. Unica is een ‘one stop shop’ voor de industrie.”
Ondertussen kijkt Twan samen met Peter Greven alweer vooruit. “We kijken nu bijvoorbeeld naar innovatieve projecten om energie te besparen. We zijn dus nog lang niet op elkaar uitgekeken.”
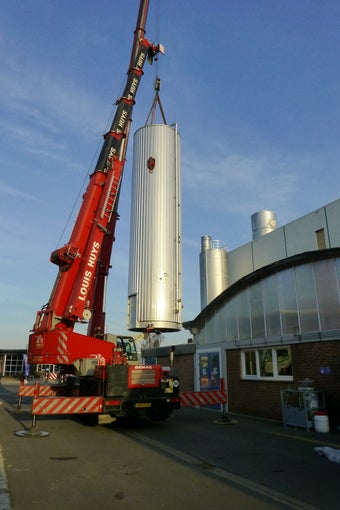
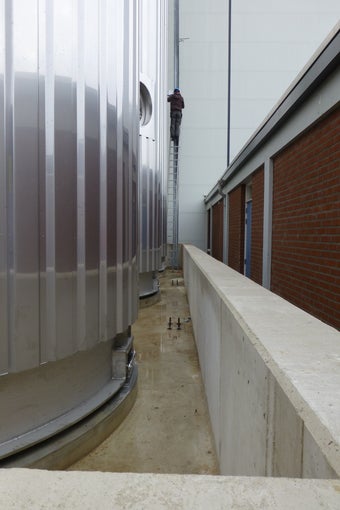
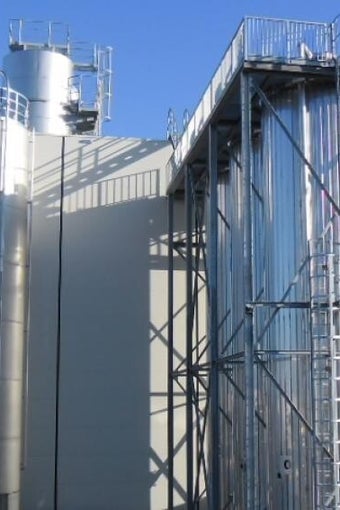
Projectleider
Als Projectleider ben ik verantwoordelijk voor het plannen, uitvoeren en afronden van projecten binnen de gestelde tijd, scope en budget. Ik werkte nauw samen met verschillende teams en belanghebbenden om ervoor te zorgen dat projectdoelstellingen werden bereikt en dat er hoogwaardige resultaten werden geleverd.
Verder was ik veelal bezig met het:
- Ontwikkelen van gedetailleerde projectplannen, inclusief doelstellingen, scope, tijdlijnen, mijlpalen en resources.
- Coördineren en motiveren van projectteams om ervoor te zorgen dat taken efficiënt en effectief worden uitgevoerd volgens de gestelde deadlines.
- het Identificeren van mogelijke risico’s en het implementeren van strategieën om deze risico’s te beperken en te beheersen.
- Opstellen en toezicht houden op het projectbudget, inclusief het monitoren van uitgaven en het uitvoeren van kostenanalyses om budgetoverschrijdingen te voorkomen.
- Waarborgen dat alle projectresultaten voldoen aan de gestelde kwaliteitsnormen door middel van regelmatige kwaliteitscontroles en audits.
- Onderhouden van open en regelmatige communicatie met alle betrokkenen, inclusief het verstrekken van updates en het opstellen van statusrapporten.
- Zorgdragen voor de succesvolle afronding van het project door het valideren van de uiteindelijke resultaten, het evalueren van het projectproces en het documenteren van leerpunten voor toekomstige projecten.
- Vereiste kwalificaties en vaardigheden
Verder bezit ik de volgende vaardigheden:
- Expertise in het identificeren, analyseren en beheren van projectrisico’s
- Vermogen om een projectteam te inspireren, motiveren en leiden naar succes
- Uitstekende mondelinge en schriftelijke communicatievaardigheden
- Bekwaamheid om sterke relaties op te bouwen en te onderhouden met belanghebbenden
- Sterke analytische vaardigheden om problemen te identificeren en effectieve oplossingen te ontwikkelen
- Creativiteit en flexibiliteit in het aanpakken van onvoorziene uitdagingen
- Vermogen om gestructureerd en georganiseerd te werken, zelfs onder druk
- Proactieve houding en bereidheid om initiatief te nemen om problemen te voorkomen voordat ze zich voordoen
- Bekwaamheid om duidelijke en gedetailleerde projectdocumentatie bij te houden
- Vermogen om prioriteiten te stellen en deadlines te halen